BINDER MAGNETIC and ADE WERK: A proven partnership
We have been associated with ADE WERK since 1992. This partnership, which has lasted for more than 30 years, has enabled us to provide numerous technical solutions for the transmission of movement in industry and other varied fields.
In 2000, the first French installation of electromechanical actuators for inland waterways was built on the Rhone-Rhine canal in collaboration with Voies Navigables de France in Mulhouse. Since then, many river projects powered by electromechanical actuators have been completed.
Areas of application for which ADE electric actuators are specially adapted:
- Dams, flap gates, weirs and valves.
- Gates, leaves gates, sluice gates and guard gates.
- Bridges, fishways, flood gates.
The company ADE WERK
ADE WERK is a company specialised in the manufacture of electric actuators for industry and the most demanding fields: nuclear, maritime, river, etc.
As the European and world leader in electric actuators for river applications, ADE has completed more than 175 works, which is equivalent to approximately 1500 actuators in operation in Europe.
The first electromechanical actuators were installed in 1995 and have been deployed in France since 2000.
How an electric actuator works
Binder Magnetic offers a complete range of actuators for all types of applications, from industrial applications to the most extreme applications such as inland shipping.
Our custom-built electromechanical actuators are the most suitable cylinders on the market: they are capable of pushing or pulling loads ranging from a few hundred kilos to 150 tons or more!
Description of an ADE electromechanical actuator
1. Drive system
The drive system is the motor system that provides the torque needed to set the electromechanical actuator in motion.
2. Belleville Washer Damping System
The integrated spring washer system protects the actuator from accidental axial shocks and jolts on the rod from the work to be moved.
3. Bearings
Used to support and guide the drive shaft in rotation.
4. Piston rod nut
The piston nut allows linear movement by converting the actuator torque into a linear axial force.
5. The actuator barrel
The actuator barrel guides the rod. It ensures the mechanical protection of the system and the IP68 sealing against external elements.
6. Actuator rod
The actuator rod is attached to the piston nut and provides the push-pull movement.
7. Actuator rod guide
The guide system ensures both rod guidance and sealing. The mechanical system is thus protected against dirt and other aggressive external media.
8. Swivel- / fork head
The fork / ball joint allows the mechanical connection and transmits the force to the mechanical system to be set in motion.
The advantages of electric actuator technology for inland waterway structures
Simple installation
- The compactness of the equipment and its discretion allow a good integration in the environment
- Only a connection to the three-phase electrical network is necessary for the implementation of the actuators
Low maintenance
- Annual maintenance: lubrication at the points provided for this purpose
- Every 10 to 12 years: ten-yearly revision to replace seals and sealing systems
- 30-year service life: all components have been designed for a service life of approximately 30 years
ADE actuators: a high-performance shock absorption system
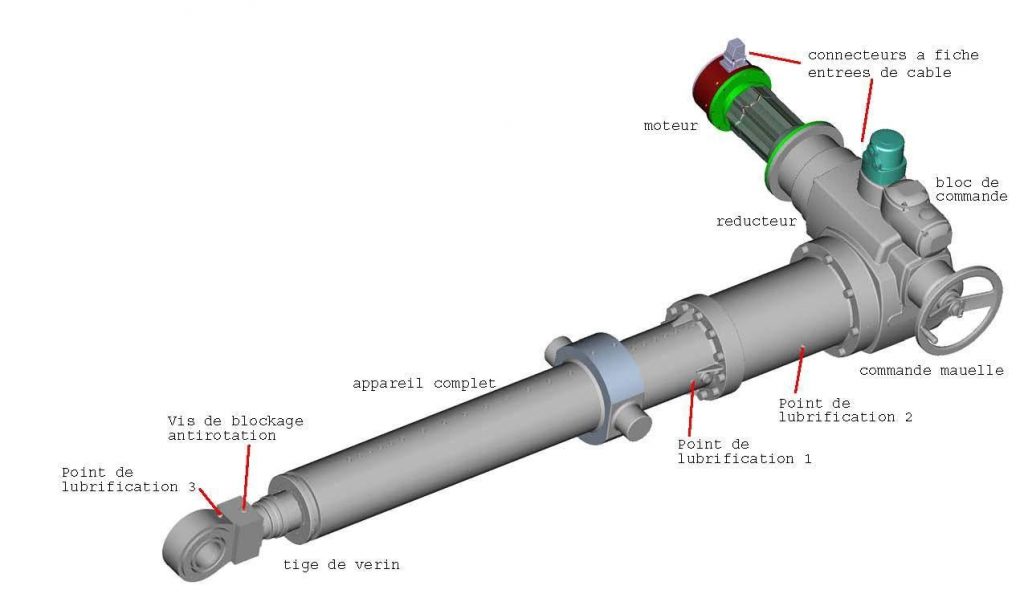
ADE actuators for inland waterway applications have an integrated shock absorbing system.
The secret of this damping system lies in the use of integrated Belleville washers that protect the actuator from accidental stresses on the rod caused by the structure to be moved.
These stresses can be of various kinds: vibrations, shocks and jolts, water hammer, etc.
As they are inherent to the operation of waterway systems and structures, these stresses often cannot be eliminated: a damping system is therefore necessary.
How does this damping system work?
The internal damping system absorbs the kinetic energy and shock wave from a jolt by compressing the Belleville washers.
The electromechanical parts that will carry out the movement in the electromechanical actuator and servomotor are thus effectively protected and isolated from the vibrations caused by the mechanical system.
The damping system operates in both directions, thus ensuring optimum protection of the electromechanical actuator, regardless of whether it is being pulled or pushed.
All-electricity: a sustainable development approach
There are several types of actuators for inland waterway applications:
-
Hydraulic actuators
- Electric or electromechanical actuators
By their nature, hydraulic actuators are susceptible to leakage, which can present a risk of water pollution.
Older electromechanical drive systems were not without risk either. These actuators, consisting of open reduction stages, pivoting segments and open drive screws or linear racks, required regular lubrication with open grease and were therefore a source of pollution.
ADE's electric actuators do not have these disadvantages and comply with water protection legislation.
Our electromechanical actuators are therefore part of a sustainable development approach and respect for natural areas:
-
Simple and discreet aesthetics that blend into the environment
-
Quiet operation of less than 55 dB
- No water pollution